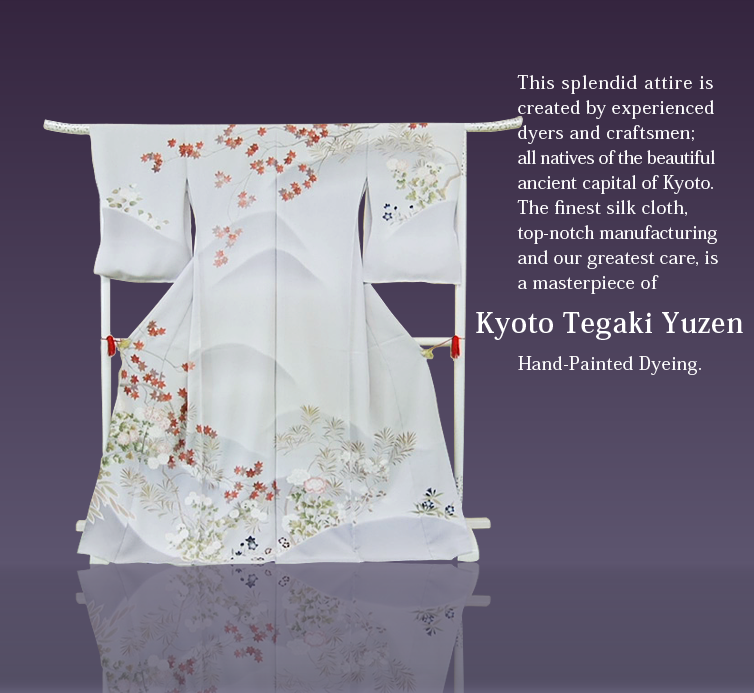
The history of Kyoto Yuzen Dyeing dates back to Genroku Period (1688-1704). An artist, Miyazaki Yuzen (of SENSU, or a Japanese folding-fan) lived near Chion-In Shrine and created his unique technique that could dye a novel design on a kimono in the picturesque, free-line, and color-free style.
In those days, the Bakufu (the feudal government) imposed restraints to make common people's lives less extravagant. Any flamboyant types of kimonos, such as embroidery inlaid with gold and silver, or tie-dyed kimono with, so called, So-Kano-ko, (a hand-painted deer pattern) were strictly prohibited. Consequently, it was not until the middle of the Edo period, in the prosperous era of merchant-class culture, that Yuzen Zome(dye), which had more colourful and picturesque design patterns, came into fashion.
There was also a point to see that ”Hinagata-Hon”( a model form, or a sort of style book of today) played an important role on spreading Yuzen zome.
The book contained some forms of designs and detailed descriptions about fabrics and colors. The way of using Hinagata-Hon itself was not new in those days, but since the Hinagata-Hon for Yuzen-zome was edited by Master Yuzen (1692), its dyeing patterns and technique encouraged the spread of the style and have blossomed into the magnificent, gorgeous style of the present Kyo-Yuzen.
Having been born and raised in Kyoto, and having seen and touched the surroundings of the town culture, a SenSho-Master of Kyo-Yuzen dye has given himself over to creating as many original and proactive fine works of Kyo-Yuzen as possible.
The manufacturing process of Tegaki-Kyo Yuzen, hand-painted Kyo-Yuzen, is based on the division system of at least 10-15 work stations, such as designing, pattern-drawing, glue-putting, brush-dyeing, color-inserting and the like. The Yuzen, therefore, is the compilation of techniques and works of skilled dyeing craftsmen, led by their master, SenSho, or a managing producer who can create original designs by unifying and coordinating the functions of all work stations. SenSho is also a dyeing designer who adores Kimono clothing with a profound sensitivity and knowledge.
Specific task process of SenSho is: first, designing based on client`s preference or SenSho`s own design plan, selecting fabrics and manufacturing process, then choosing relevant craftsmen. Here it is very important to carefully sort out the right artisan in the right station, because even skilled artisans vary in terms of art sense and characteristics.
SenSho`s quality of leadership greatly affects product-image makings. So, coloring scheme, gold-application, embroidered figures, or detailed final checking, is greatly cared for by this dyeing master, SenSho.
The total coordinated image of a product and a good workmanship are indeed indispensable.
Tegaki-Yuzen tasks are completely done on a division basis, specializing in superior skills at each work station. Then, the best accomplishment at each stage and its integration into the whole is truly essential to produce a fine piece of Tegaki Yuzen.
Native water in Kyoto is a soft type, the quality of water is without a peer in the world. This is probably why the fine dyeing industry has become so highly developed in Kyoto.
The craftsman`s invisible fastidiousness is inlaid everywhere in kimono, nevertheless, traditional Tegaki Yuzen feels at a time gorgeous, graceful and dignified with a rather daring sense of color.
Yoshikawa SenSho Company wishes that it is Kyoto-Tegaki Yuzen can authentically represent Kyo-Yuzen Dyeing, and believes that the SenSho dyer, born and raised with traditionally skilled craftspeople, can work together to create a splendid kimono with a great care, choicer fabrics and top-notch dyeing skills.
KYOTO, the ancient capital of Japan for over 1000 years.
Eminent sensibility, traditional culture, the people`s nature, and its long innate familiarity with quality (without intending to), are all gifted to only the people living in this city. This is the very pride and credit Kyoto confidence has long nurtured.
We always try to embrace the feeling of the era when Miyazaki Yuzen established his unique dyeing world and to keep its original spirit of Yuzen dyeing by constantly renewing precise production standards.
Yoshikawa SenSho Company states to makes tireless efforts to realize its principle that Kyo-Yuzen kimono must be equipped with spatial effect, silky delicateness, elegance, quality of textures, while conserving its traditional dyeing techniques.
Combining Tegaki-Yuzen with Tie-dyeing has long been believed to be impractical.
Yoshikawa SenSho and their craftsmen, however, have enabled us to combine these different dyeing systems and have been successful in expressing more elegant quality of textures with this method. This success stems from the fact that our SenSho Masters and dye craftsmen over four generations have invented various new types of techniques. We succeeded in dyeing many different types of colors into a solo Kimono in a perfect and harmonious way.
Success of this combined use of Tegaki Yuzen and Tie-dyeing largely depends on the introduction of Division-system and Resist-dyeing skills that we invented. The success of solving this difficulty has also greatly contributed to development of Kimono dyeing technique in this country in many ways.
Both Itome Yuzen, a method of resist dyeing, and tie-dye require a complex product processing and advanced techniques. It is very difficult for a single craftsman to master all different skills of the work-stations, we, therefore, generally introduce a system that fixes one specific specialist at one work-station. In other words, it is this division work system that has created such advanced dye techniques and high degrees of professionalism. In fact bringing in plural types of methods under one manufacturer is not at all easy.
Yuzen and Tie-dyeing both require individual techniques in the resist-dyeing method, and consequently, mixing of these different dyeing skills brings out complicated technological difficulties.
Major Problems of Cross-Dyeing of Yuzen dye with Tie-dye
1.The sensitive resist-dyeing of Itome-Yuzen will impair layers of Yuzen because
the tie-die resist uses high pressure.
2.Yuzen resist-dyeing, that can only protect one-way penetration, will be
universally dyed by the resist-dyeing of the tie-dye that has a penetration
characteristic.
The Resist-Dyeing by Glue (to sustain the penetration of colors) is the most featured dyeing technique in Tegaki-Yuzen. This technique was then unprecedented, and it can create picturesque lines of free-curves, or variety of characteristic dyeing colors. With the invention of this technique, Kimono has become an even more refined and elegant, splendid, magnificent garment.
Over 300 years of ceaseless efforts and technical innovations by its artisans, the Yuzen dyeing technique has reached the present-day apex that Kyoto can be proud of worldwide. Therefore, the traditional beauty of the style invented with this dyeing technique is timeless and still admired by people.
There are about 10 work stations in Kyoto Tegaki Yuzen manufacturing, and each station is perfected by highly specialized craftsmen. Here, the oversight of SenSho Masters with their distinctive production images are fused into the function of each work station and become essential for creating elaborate work at each station. Otherwise the total completion of these magnificent works cannot be expected.
The following are the work processes of our manufacturing systems that produce Yoshikawa SenSho`s technical fastidiousness.
Painting with a brush soaked in flower sap, called AoBana-Tsuke (indigo blue-flower juice).
First, sketch a planned pattern with the brush dipped in the sap of indigo made from petals of dayflower; soaking it into the fabric by properly wetting the part with a small piece of wet Japanese paper, or Washi.(※1)
We maintain the constant training of sketching and drawing scenery. Here, a best-fit artist is selected for a motif of every pattern.
※1 Recently, a chemically-created artificial dyeing ink, that can erase color afterwards with heat, is also sometimes used.
For protecting a pattern against dyeing, a rice-bran glue is placed onto the contours of its design with a fine paper-tube pen whose nib is equipped with a brass bar. Here, elaborate work skill is required to maintain a given-thickness of line consistently. This type of line is called “ItoMe” (or a thread-like fine line), and after dyeing work, the white ItoMe line is seen along the outlines of patterns(※1), which is one of the most distinguishing features of Kyoto Yuzen Dyeing.
There are two sorts of ItoMe-resistant: a rice-bran glue that is to soften its finish, and gum glue (※1) to express a more edgy appearance.
※1Glue strings: The finish becomes soft. Rubber strings: Expression with the effective sharpness of the corner is possible.
On the stage 3, the work called, ”FuseKo” (or applying glue evenly to the whole part of the patterns) where Yuzen dyeing is later to be laid, after ItoMe (work stage 2), and then Hiki-ko (ground-powder) is dusted over the glued parts. This task plays a role of protecting the patterns against from dyeing on the brush-dyeing stage(→4). At this moment it is important to select an appropriate kind of glue, suited to the density of brush dyeing. (example: Jho-neba, or more sticky glue, for thicker brush-dyeing is used, because it needs thicker glue with a strong adhesiveness).
A length of Kimono cloth is stretched by its ends, with the designs drawn on it, a craftsman goes on to apply dyestuffs with hair brush. First, he dyes the lighter color a number of times with his brush to the degree that he can make its color darker. For this work highly skillful techniques and many years of experience is desired. Technique differs day by day, for instance, due to humidity, to the quality and condition of the dye; requiring a shifting of balance in all materials used. This elaborate art of hand-painted work is one of the prides of traditional Japanese craftsmanship.
Hiki-Zome is the most fastidious process, which we value greatly. Furthermore, a three-dimensional image that Kimono dyeing can reveal, is perfected by the gradation effect of Kyoto Yuzen Dyeing.
After the completion of Brush dyeing, the work moves onto the next process;
the steaming of fabrics painted in stage 4. The fabrics are put in the box and steamed in the heat of about 100 degrees centigrade, for from 20 to 50 minutes to settle the dyed color of the fabric. The fabrics of darker colors, in particular, will be repeatedly steamed.
The fabrics that have just been through the steaming process and are now ready for coloring, move onto the cleaning stage: it is vital that the fabrics, which had been painted, glued, and dyed in the past stages, should be washed clean away with plentiful clean water. Any excess dyes, glues, or powders have to be removed by rinsing them out in the water.
By the time that a roll of Kimono cloth has completed its dyeing, the cloth must be passed through water several times. It is probably for this reason that Kyo-Yuzen Dyeing is called, “Art of Water.”.
Next comes the work of dye colorant, with ink brushing in the areas where the pattern contours that appeared after washing away the glue, is applied. This work stage is called, “Iro-Zashi”(Color-Inserting). Color is painted from light to dark, in that order. Occasionally depending on brushwork, gradated patterns (Ombre-dyeing) are implemented.
Nowadays, chemical dyes are most commonly used, but formerly some plant dyes, like Ai (Indigo), Benibana (saffron), Akane (madder), Shikon (Lithospermum root), or Kariyasu (Miscanthus tinctorious), as well as natural dyes from insects were also used. On this work stage, most of the colors used for patterns on a kimono are painted. When one color is dyed, its color will spread and blur, so to prevent the mixing of its blur with the next color, there needs to be some intermission: we wait until a single color dries before proceeding.
The dyers in Yoshikawa SenSho Yuzen skillfully use edgy blushes, called a KataHa type blush or the single-feathered whose hair-ends are diagonally angled.
Fine and uneven gradation dyeing is perfected with a brush whose longer side has dyes applied while the other side has glue-water. Here, a quick speedy and precise techniques are really a prerequisite.
On the color inserting station (WS-7), the dyes are in a state to be put on the cloth texture. Therefore, in order to set the dyes on the cloth and attain a fine color development, a steaming process of over 80 degrees centigrade for 20-40 minutes is required. After this steaming work, Kihatsu suisen (thinner rising), Mizumoto (washing-away in water) and Yunoshi (steam and iron) are processed, then is transferred to the final station of dye work.
We try to express a distinctive gorgeousness by applying gold or silver foil and powder onto the patterns. The authentic beauty of Kyo-Yuzen is traditionally kept by using the techniques of KanaKukuri (golden effect), OshiHakusuzuriHaku (grinding effect), or gold-silver dust. The wide range of gold-coloration covers many types of foiling, such as, HakuBokashi(gradated foiling), ItomeHaku (fine-line foiling), OshiHaku (pressed foiling), Sunago (gold/silver dust), SuriHaku (sliding foiling). These techniques are freely selected to make full use of the nature that the fabrics or patterns convey to the atmosphere.
This process of gold-coloration is able to use a fine glue tube, a stencil, a bamboo tube, foiling sticks, and so on, to provide a glittering and encouraging scene that can make a viewer instantly fascinated.
Yoshikawa SenSho occasionally uses genuine gold foils to give textures superb looks.
Graceful, splendid, and voluminous sense is added onto the patterns by embroidering silk, gold, and silver threads. In Yuzen Dye, the final, accessory processing (gold and embroidery) is called, “Ashirai,” (a reception treatment). Our final objective is, therefore, to complete Yuzen Kimono dyeing with beautiful, elegant, and attractive effects, by performing stitching into a flat world of fabrics. We might be able to compare this process to the application of women`s make-up. In embroidery, there are various types of techniques, “KomaShu” (gold foiling),“SagaraShu,”( stitching),”MatsuiShu,” (stitching), “Kasuri,” (gradation), and TakeyamachiShu,” (Takeyamachi-street pattern).
From among these ample types, to select an optimal type of stitching for a motif that the design requires the practice of our craft artistry.
What is Supremacy of Kyo-Yuzen ?
Elegant sensitivity, gifted to a people who have lived in this beautiful ancient capital of Kyoto for over a thousand years. It is a genuine sense of the residents who are blessed with its long historical and cultural climate. We believe that this treasure, along with years of skill experience of craftsmen enables us to create the dignified, splendid supremacy of Kyo-Yuzen.
Yoshikawa SenSho has long produced unique and original beautiful Kimono, blending our own versatile techniques extensively in every place.
Here are some supreme works of our Kyo-Yuzen artists.
1.click to enlarge the images
2. image moves back and forth with [Prev] [Next]
※place the cursor to see the enlarged photo
expressing freely the trend of the times with novel ideas and techniques handed-down for generations collaborative projects of Kimono creation with superb Kyoto craftspeople believing in brilliant future of Kimono and Kyo-Yuzen continuing to search for an excellent sense of value and perfection of costume beauty being as a supreme dress maker of “Real Clothes” KIMONO promising to provide beauty, liveliness and confidence to our clientele
Firm Name | Yoshikawa SenSho Co. Ltd. |
---|---|
Address |
◆Head Office 492-12 Naka Tsutomu-cho, Senbon Higashi iru-sagaru Shimotachiuri-dori Kamigyou-ku, Kyoto city [ZIP] 602-8158 ◆Northern Sales Office 149sieruriberute201, Taishogun Higashitakatsukasacho, Kita-ku, Kyoto city [ZIP] 603-8333 |
Contact | Phone.075-465-5656 Fax.075-465-5657 |
Access | |
President | Hiroya Yoshikawa |
Established | 1897 |
Incorporation | 1963 |
Business Operation | Yuzen Business Cloth Dye Processing |
Started his business of Tegaki Yuzen in 1897, independently of his brother, Yosakichi.
His brother also managed a business related to drawings and dyeings.
Yosakichi was famous for his creation of KakeJiku, a Japanese style hanging roll,and associated with the famous painter then, Takeuchi Seiho.
He had the training for Yuzen dyeing, at a very noted Yuzen manufacturer(which was 460 years old then).
In 1930 He started to practice his own dyeing business of Jyuban(undergarment).
The factory was closed for the duration of the war. About 10 years later, he restarted the business of Kimono dyeing based on the pattern style.
The company was incorporated in 1962 and named Yoshikawa SenSho Co.Ltd.
He entered the Yoshikawa Yuzen company and started being a trainee in its factory.Between 1960 and 1973, he mainly dealt with “ChakushakuSuriKomon,”(casual Kimono with gold processing) that was thought the top-class design in those days. After 1975, he created “Chakushaku”(casual) that was produced using the combination dyeing of sliding foils and the tie-dye, and received quite a lot of orders, making a version of KanoKo tie-dyeing or a formal wear of Okeshibori Chakushaku (casual tie-dye in a pail).
1997 | Kyoto Governor Award |
---|---|
1998 | Kyoto Dyeing and Weaving Laboratory Award |
1999 | Kyoto Board of Commerce Award |
2000 | NHK Director Award |
2001 | Kinki Economy and Industry Development Bureau Award |
2002 | Minister of Economy, Trade and Industry Award Kyoto Governor Award |
2003 | Kyoto Board of Commerce Award |
2004 | Kyoto Governor Award |
2005 | Kyoto Mayor Award |
2006 | Dyeing and Weaving News Magazine Award |
2007 | Tango Textiles Industry Guild Director Award |
2008 | Minister of Economy, Trade and Industry Award |
2009 | Kyoto Board of Commerce Award |
2010 | Japan Traditional Dye-Craft Conservation Corporation Award 100-Selection-Exhibition of RinPa School Award / Kyoto Mayor Award |
2011 | Minister of Economy, Trade and Industry Award 100-Selection-Exhibition of RinPa School Award /Kyoto Governor Award |
2012 |
Minister of Economy, Trade and Industry Award 100-Selection-Exhibition of RinPa School Award Tango Textiles Industry Guild Director Award Traditional Craft Industry Development Association Award |
2003 | Exhibited a new type Japanese-style folding screen on which Kyo-Yuzen dyeing and Kyoto-Lacquer-ware painting are collaboratively fused, held at the Monza-Trade fair in Italy, under the support of Kyoto City Presented the American movie star, Tom Cruise with Japanese men`s Kimono at the chance of his visiting Nijo Castle |
---|---|
2006 | Exhibited our products at the Atmosphere-Trade-Fair in Paris, which showed the mood-dresses with basic tone of the real Yuzen dyeing method |
2008 | Released the collaborative new bags with MORABITO, high-end French Brand,in the Exhibition held as the commemoration of 150th Japan-French Friendship |
Please feel free to ask any questions or opinions through the following